Silicon Moulding Services for Customized
Advantages Of Silicone Molding
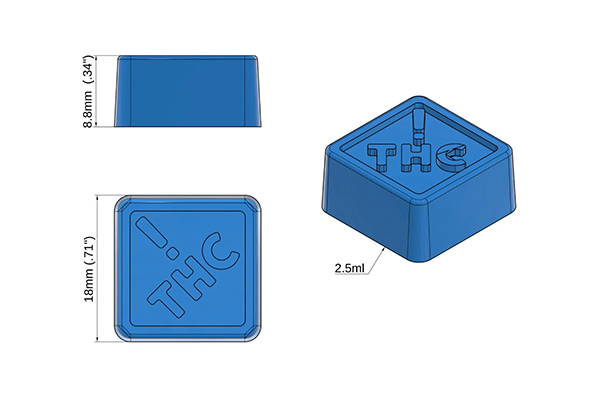
Prototyping
Small Batch
Low-Volume Production
Short Lead Time
Low Costs
Applicable To Various Industries
What Types Of Silicone Molding Can Be Produced?
1: Design
Every part – no matter the materials used – begins with a design. If you have a CAD file you can upload directly to our office but if not, feel free to ask our designers for help. Silicone reacts differently than other manufacturing materials; ensure your specs are accurate before producing thousands of units.
2: Mould Creation
Like plastic injection moulding, GUAN SHENG moulds are produced in our own factory, saving time and money. First a master model is produced via CNC or 3D printing. Then a silicone mold is created from the master model, which can then be used to quickly produce up to 50 duplicates of the master in a variety of materials.
3: Silicone Part Casting
Mould are injected with silicone the same way plastic injection injects polymers but with a key difference: unlike plastic injection molding where materials are heated and injected, LSR is chilled and injected into a heated mold, then cured. Cured silicone parts will not melt or warp when subjected to heat.
Producing Silicone Casts
LSR are also considered as the material of choice for industries such as Automotive or Medical devices for which small and complex elastomeric parts needs to be produced at high speed and optimum productivity. In such cases, Liquid Injection Molding of LSRs becomes one of the most efficient process to fabricators.
Silicone moulded parts can be created for prototypes, in small batches, and for low-volume production. The following pieces of information will help you decide how you will want to produce your silicone parts:
Quantity – How many will you need?
Tolerance – What does it need to do?
Applications – What will it need to withstand?
3D Printing of Silicone Parts
Many projects require multiple prototypes be made quickly. If you need 1-20 simple silicone casts made in just 24-48 hours, call us and explore what 3D silicone printing by GUAN SHENG Precision can do for you.
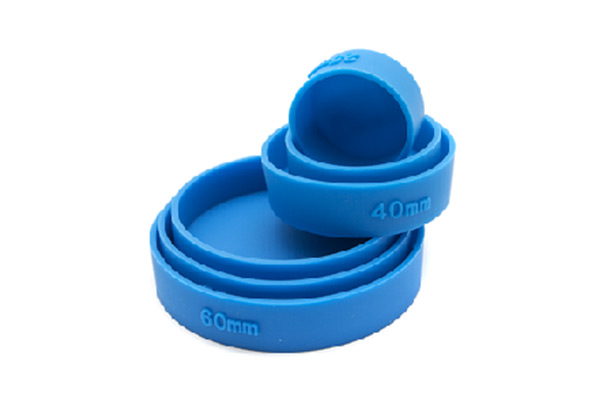
Silicone Casting
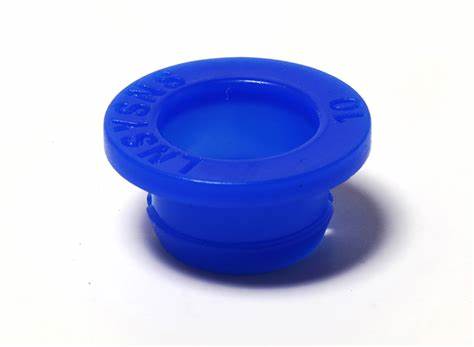
Using non-metallic moulds, high-quality silicone castings can be produced using a range of colours. For a dozen to a few hundred units, silicone casting offers a less-expensive option when compared to producing metal parts.
Silicone Moulding
When you need high-quality prototype parts made in small quantities, liquid silicone rubber (LSR) moulding is the fast and economical solution. A single silicone mould can be reused, producing up to 50 identical casts quickly saving time and money – parts are easily reproduced without additional tooling or design.
The Liquid Silicone Moulding (LSR) Process
For small-batch and low-volume manufacturing of silicone casts, liquid silicone moulding is the fast and reliable manufacturing process. Thousands of identical moulds can be reproduced quickly using a single design and only one mould for expedited delivery of your silicone rubber parts. LSR is available in a wide variety of colours, has reduced weight compared to metallic parts, and is extremely resilient.